DIY Wooden Toolbox Plans For Crafting Simple Storage Chest
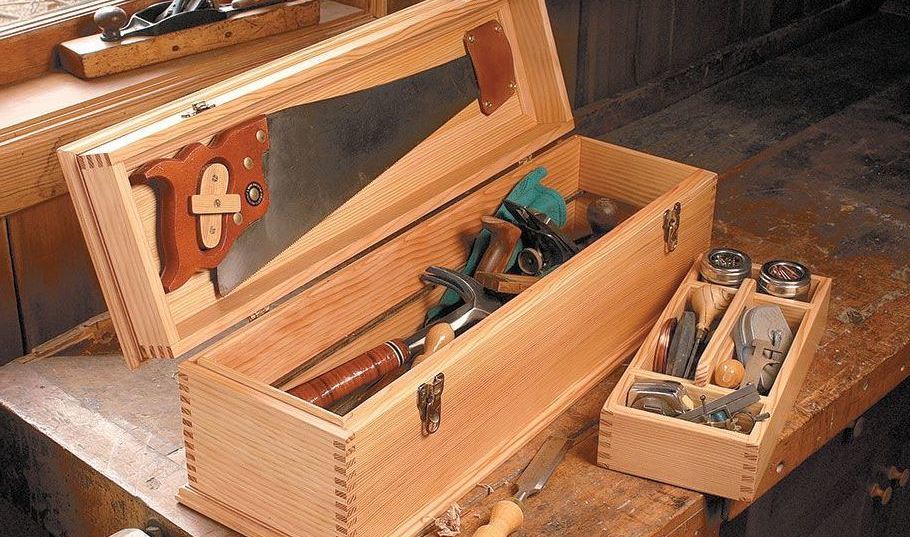
Steps for constructing wooden tool tote
Check out the guidelines on the bags, or look at manufacturers' websites to find out if any (https://woodworkingdrafts.com/diy-wooden-tool-chest-plans-blueprints) of the specific mixes will best suit your project. The swing must be properly secured to support its weight and the persons who would be occupying the swing. You won't likely get this molding in the home center, but you could request it from a specialist or pick a similar style. Screws are more effective than nails on the clamp board for making it easier to change the liner in the future. This method is more effective when right-handed people use circular saws with a motor located to the right of the blade. Use all-purpose screws to attach the back rim of 1x8 and 1x2 front rim to the 2x8 block supporting it.
Be careful. Be sure to place nails between slats. It will take a long time to remove dark lines using fine grits. After cutting the posts in the center to length, you can use a miter box or miter saw to cut off points on the sides of the center posts. Drill pilot holes and then install slats evenly spaced before locking them in place. Separate pockets are left to store and sort ribbon, tape, and scissors. The hole you drill should be the biggest size that is able to fit into the space. It is possible to create drywall in the traditional method by scoring one side using a knife, bending to break it along the score line, and cutting off the backing of the paper.
It is important to ensure that the framing won't be used to block the electrical outlet. Be sure you secure the steel tightly during drilling. Expanding woodworking patterns that are scaled down to full-scale can be a huge undertaking, and results are often not precise. Use a moist rag to remove the glue from the handscrews that are taped, or remove the tape and put on new tape prior to the next job that is messy. Cut the pieces using the circular saw or Jigsaw, following the dimensions shown in Figure. Learn more about the process and how to construct it. It is also helpful to use an orbital sander that is random, particularly for sanding the sides to a smooth finish prior to placing the veneer.
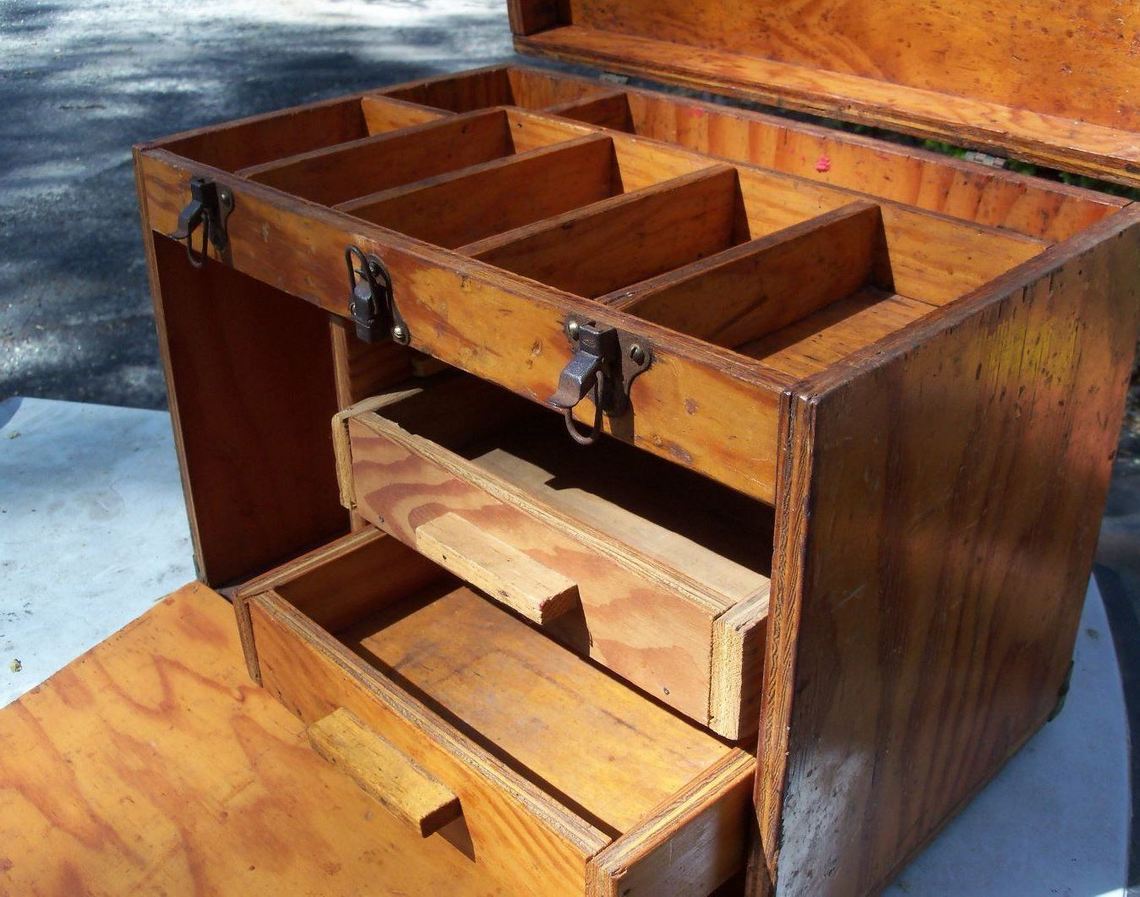
We suggest making use of small brackets for an angle to mount your shelves. For instance, if you were cutting across the sides of a board, you'd be able to move your router from left to right on the edge that is closest to the shelf. Further details are provided in the instructions and pictures below. The workspace will be large that folds away, and requires extremely little space to put away. Apply two coats at a minimum and let each coat dry. After sanding, clean the dust with a damp cloth. I had to put an inch of cardboard between the two boxes to ensure that the frames were in alignment. The shelf cleats are marked on the walls. The fact is that it works and actually seals the surfaces. The joints will twist slightly when you construct your bench.
However, they'll need to be straight and neat as you cut the joints and assemble the bench. Once the glue is dry, then sand the surface flat. As you work, problems get more complicated, and you'll get sloppy work that is slanted and lopsided. Other sizes are available but require different drill templates. Drill holes at the edges of each cutout, and then use those holes to initiate and end your cutting. The same procedure is followed by the opposite side. It's a little more expensive, but the grit will last for a longer time, which means you'll actually save money regardless of whether you're making use of discs, sheets, or belts.
Procesando video...
Attach the upper sides to the tops of the legs. Keep doing this until the plywood fits snugly in the groove. Attach the front frame in the identical fashion, then place the subtopics in the same way and screw it onto the face frame. Determine the position of the gravel pad by cutting the grass with a shovel. After that, remove beams from the way and cut sod where the gravel will be. Dry-fit the other boards by spacing them to allow for the curve. After that, you can center and secure the shelf onto the brackets and an attached strip. Create a scaled drawing of the structure adapted to your house prior to applying for the building permit. Once the glue has been set, it will make the boards stiff and strong, thereby strengthening the cabinets. This is typically the most effective source for high-quality wood boards.
You can cut them to the appropriate width and plane across all four edges. Stud finders on the internet are the ideal device for this. It is hard to think that floating shelves are made of plain cheap, heavy, and old hollow-core doors. Install the top support and the top glide so that the support is level and straight with the frame's top opening. Most of the time, this is a straightforward job, more of wiping down the surface instead of sanding it. If you're working in a chemical environment, wear a long-sleeved t-shirt and gloves to shield your skin. Make the clutch work by twisting it in front of the chuck until you reach the smallest number.
After that, fold the bill in four thicknesses and use it to place the thrust bearing in front of the blade. Then, you can drill holes then, flip it over and secure it to the other side of the front door. Do not make any craft that is able to be snagged with the blade any other way. This provided us with a safe and stable surface on which to cut grooves. You can use the same mineral spirits for multiple cleaning brushes. Examine the cabinet box for squares by taking a diagonal measurement across the corners. It's faster when you stack two parts to cut and smooth simultaneously. Smooth edges using sandpaper, and clean the residues off using the help of a damp cloth.
Pocket holes should be drilled at the two ends of the support and put between backrests. The oil finish keeps the lumber looking natural, but it's protected from the possibility of rot. Install a large amount of caulk on the plug strip before screwing in the roofing panel. Use four screws for each shelf and divider and eight screws per side. Cut the plywood board to the size of your desktop. Purchase a few additional boards so that you have more boards available as you build. Reset the guide rail and use it as well as a level to set and plumb posts within each hole. Connect one of them to the top of the headboard, with one side facing the outside and the angled edge pointed towards the middle of the headboard. For complex assemblies, allow yourself more time to work applying the slow-setting wood glue.
You can cut your molding more securely and precisely by placing the molding upside-down onto the bed of the miter saw. Make a notch in your deck boards to make them fit over the supports on the sides. This project will blend with the rest of the space better if you replace your base molding ( https://www.finewoodworking.com/project-guides/shop-projects/tool-chest-with-drawers ) with a new one and then run it along to the bottom of the bookcase. If you're staining, painting, or staining the shelves, be sure to apply the final coat of paint after they've been mounted and the moldings have been installed.
The doors are held by juniper branches made into the form of nails. Make use of weatherboard and push stick to ensure security. Cut the parts according to the dimensions and angles indicated in the cutting list found in the project details below and in the images. The jig should be moved with the cut-off blanks until you get to the end of the jig, then turn the blank around with the blade. Do not let clamps run free across the work area. Also, ensure that center slats and arches are parallel to one another using an equilateral triangle. Clean any squeeze-outs with the help of a paint scraper or chisel. Then, remove the form starting by the sides. Make sure you cut off the tube of caulk with care to leave an opening that is about them as big as a finish nail. If the assembly is bent up, place another clamp over the boards. This is why we created this idea. Guard against the rot of lumber with the right products.
When the bed cabinet is up and the frame upright, it's time to install gas springs. Then, move guides forward so that the fronts of guides are on top of the blade's gullets. The fact that you've used pressure-treated lumber doesn't mean that the outdoor project must remain green. Place the decking planks on the frame, with the woodgrain pattern facing upwards. All the materials are accessible in home stores. After that, prime and paint the bookcases according to the manufacturer's specifications. Move the form around to spread out and mix. It's simple to construct using only basic tools. After that, you can notch the front supports in the manner shown in Figure. Nearly any wood project can be completed without any glue or fasteners made of metal. Utilizing a beam compass and an old piece of cardboard, create a curve that will join the leg's intended positions.
Note the width of the workpiece at both ends of the sheet. A handsaw is fine, but smaller is best. Install the door frame using pocket screws as illustrated. Simple cardboard sheaths bonded using duct tape can complete the task. Reduce eye strain while searching for the right socket or wrench.